Intern at Shaw Industries
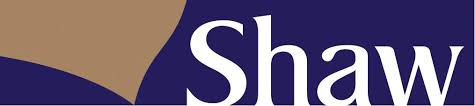
This summer, I have had the privilege to work for Shaw Industries at Plant 78 in Aiken, SC. Shaw Industries is the world’s leading commercial carpet and hardwood manufacturing company based out of Dalton, GA. Shaw Industries also manufactures tile, resilient, laminate, and sports turf (They have installed turf for the Baltimore Ravens game and practice fields, as well as numerous college football and baseball stadiums!) The plant I am working at is a fiber manufacturing plant. Our plant has four main processes: Polymerization, Extrusion, Twisting, and Heatset. In our polymerization process, we produce Nylon 6 chip from Caprolactam. The Nylon 6 chip is then sent to our Extrusion department, where it is extruded into a single-ply strand of fiber and strengthened before being sent to the Twisting department. In Twisting, two single-ply ends are corded together to form a two-ply stand of fiber and then sent to Heatset. In our final process, we add texture to the fiber and send it through an oven in order to set the added texture. Once the final product is complete, we ship the fiber off to another plant, where it is tufted into carpet and dyed to meet customer requirements.
While I have worked on projects throughout most of the processes this summer, my main focus has been in the Extrusion department, tackling an issue we have with our winders. The winders are used to take the extruded yarn and wind it onto a plastic tube for the next processes. Winders are our leading cause for broken ends, which leads to production downtime. Currently, there is no method to automatically track winder performance and catch problem winders before they cause any excessive downtime. Working with our mechanics and outside contractors, I have designed a database that will automatically track winder performance and display it on monitors in our winder shop. With over 100 winders to track, this database will be a vital part in troubleshooting winders, ultimately leading to better preventative maintenance and lower production downtime. As of now, we are waiting on a bid from a contractor and vendor. Once the bid has been received, I can finalize the capital project and we will begin ordering parts. This project will be completed by the end of August.
I have had nothing but great experiences working for Shaw Industries. While I have only worked two terms at Plant 78, I have worked with other Plants on various projects and can see what a great company Shaw is to work for. Co-ops are treated like full time employees and are given meaningful projects that play a critical role in keeping our Plant functioning on a 24-hour basis. Whether you are a chemical, mechanical, or electrical engineer, Plant 78 will make sure you are constantly on your feet working on something significant.